WEIMA's Highly Efficient
Dewatering and Press Series
The WEIMA drainage and press series contains label presses, can presses, recycling and packaging presses, hygienic design presses and chip presses. Highly efficient machines for businesses and facilities looking to reduce liquid weight and volumes to save on waste management costs.
KEY ADVANTAGES
Efficient, Affordable and Secure In-House Solutions
-
Low investment cost
-
Compact Footprint– from 3 m x 1.5 m only
-
Hygienic design - stainless steel execution
-
Minimal energy requirement
-
Simple, flexible installation
-
High through-put: up to approx. 3000 cans/h of 330 ml can size
-
Save on waste disposal
-
Hygienic design in place for drained seperated liquid in G.300 Duo
WEIMA - C. Series Drainage press for metal and plastic swarf
Hydraulic drainage presses present a environmentally-friendly, efficient, and cost-effective method for effectively dry, dispose of or resell shavings that are produced during machining. The C Series dewaters and compacts all common metal chips including aluminum, steel, brass, copper, bronze and more.
The WEIMA C.200 produces discs with a diameter of 200 mm – completely without a failure-prone auger. Chips, which are produced during turning, milling, drilling or other machining operations, are pressed and then transported further into a container with low dripping.
The expressed cooling agents, emulsions, or oils can be reclaimed and reintegrated into the machining process.
Simple Installation as plug-and-play solution
In order to make installation as convenient as possible, the C series presses are preset and delivered ready for operation as a plug-and-play solution. The machine can be easily integrated with existing machinery by the use of height adjustable machine feet allowing the filling height to be individually adjusted. All that is required for installation is a power connection and the alignment to the up-stream processing machine.
Compression Advantages
Since the compressed chips have less residual moisture, their weight is decreased and in some cases the scrap value is increased. Depending on the material, compression ratio can be as high as 10:1. This reduces handling and disposal costs to a minimum.
Compact Discs Thanks to Conical Ejector
Two half shells on the conical discharge pipe, which are closed by disc springs or hydraulically, allow the chips to be pressed into discs with a diameter of 200 mm.
Worry-free Automatic Operation by integrated sensors in the hopper
Using integrated sensors in the feed hopper, the press can function automatically. When a predetermined level in the hopper is reached, the press automatically turns on. To reduce wear and tear on the machine components, the press automatically stops as soon as the hopper level falls below a pre-set level.
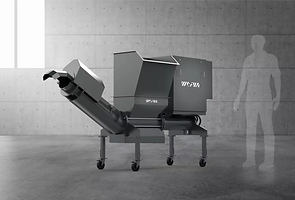



WEIMA - E.Series Dewatering Press
Drainage presses of the E series work electro-hydraulically by means of different hydraulic cylinders. The material is fed manually through the curved feed hopper. The pressed out liquid or paste is collected in a collecting trough and can be drained by a separate pump.
Flexible set up thanks to lockable rollers
The compact presses of the E series can be moved on lockable rollers to the respective place of use and can be used there directly. Temporary use outdoors is also possible, as the machine has been designed according to IP 65 standard.
Simple operation and fast parameter adjustment via Siemens PLC control
Parameters (e.g. pressing time, pressing force) can be quickly adjusted via the colour display of the built-in PLC control. The re-pressing function can also be set in a user-friendly way via the PLC control. This programmable holding time is particularly necessary for pressing absorbent materials.
Ready for multi-shift operation due to oil cooling with heat exchanger
To compensate for temperature differences in the hydraulic oil, machines of the E series have an oil cooling system with water using the heat exchanger method. This ensures long operating times without downtime. The heat exchanger is installed in the hydraulic housing and to protect against contamination.
Increased discharge height of discs for flexible discharge into containers
The inclined discharge pipe allows the formed discs to be discharged at an elevated level – directly into a large bin or tipping trough. This saves the use of a conveyor belt. Depending on requirements, the discharge pipe can be configured straight, to the left or to the right.
Good accessibility for cleaning and maintenance due to flexible installation and maintenance hatch
Thanks to brakable rollers, the E series machines can be used flexibly during operation. This ensures optimum access to the machine also during cleaning and maintenance.
Collection and targeted discharge of liquids via the drain pan
The drain pan, which is located under the press, collects the drained liquids. Depending on the installation of the machine, these run off from there directly into a drain or can be drained off with the aid of a hose via the milk pipe fitting.
Maximum safety during loading due to curved hopper design
The curved hopper prevents cans or other materials from escaping from the machine during the pressing process due to the enormous pressing force. In addition, the curved shape facilitates cleaning and prevents uncontrolled spraying of pressed-out liquid from the filling opening.






DID YOU KNOW?
To ensure the long-term use of the WEIMA Drainage and Press series, high-quality stainless steel is used.
This protects the machine body and the control cabinet from wear and corrosion while simultaneously remaining low-maintenance and hygienic.
Weima G. Series Recycling or Hygienic Design
With the WEIMA G.200 you receive a modern high-performance press for the draining and subsequent compressing of food, beverage and detergent packaging and containers. The drainage unit presses up to 4.2 m³ of material per hour with a degree of pressing of up to 99% into handy 200 mm diameter pellets. These then only have a residual moisture of 3 - 30%. This is ideal for further processing in downstream recycling processes.
Flexible discharge due to increased discharge height and individual discharge length
The length of the discharge pipe can be extended individually up to five meters. In contrast to a screw press, no conveyor belt is necessary for the discharge into a container or a tipping trough due to the increased discharge of the WEIMA presses. Thus, the press can be optimally placed according to your spatial requirements.
Different hopper sizes for every application
You have the choice between different hopper volumes: 220 l, 600 l, 800 l, 1,200 l or 2,000 l. In addition, a manual or automatic hopper lid can be fitted as a safety and hygiene protection.
Hygienically flawless thanks to optional hygienic design
Safe and clean. Thanks to the cleanable design, WEIMA drainage presses maintain food safety, meet hygiene standards, and simplify cleaning procedures. This means that down time can be minimized.
Multi-shift operation possible through hydraulic oil cooling
The use in automated multi-shift operation is possible without any problems. Thanks to oil cooling using the heat exchanger method, the hydraulic oil can be kept at a constant operating temperature without overheating.
Easy cleaning and maintenance thanks to optional pre-cleaning system and maintenance hatches
If required, the machines of the G series can be equipped with a pre-cleaning system. A multitude of nozzles mounted inside the press pre-clean the press and loosen coarse material residues. This simplifies subsequent manual cleaning. Five maintenance hatches facilitate access to the machine for cleaning as well as any maintenance work.
Optionally, the use of a fully automatic cleaning system is possible. This integrated cleaning system cleans the drainage press automatically. Nozzles inside the machine clean the press at a rate of up to 20,000 l/h. The integrated software controls the process.
No material bridges thanks to horizontal agitator
A horizontal agitator in the feed hopper can be selected as an option. Continuous material circulation prevents bridging in the hopper and thus ensures constant material feed.
Individual screen sizes for all types of packaging
The wall of the pressing chamber is perforated to allow the emptied liquid to drain off. The sieve size can be individually adapted to your material properties. For pasty materials such as yogurt or sour cream, round holes up to twelve mm in diameter are usually selected. For liquids, on the other hand, sieve holes as small as 4 mm are possible. In any case, it is important that fine particles from the packaging do not get into the drain pan together with the liquid.
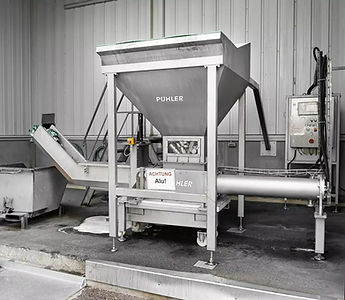
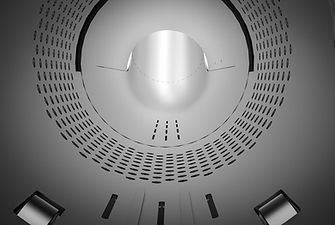
Chamber walls that can be individually adapted to material properties up to 12mm
.jpg)
Perforating rollers for gentle opening of packages


Suitable for all kinds of packaging applications:
Tin cans, Liquid Paper Board, Pouches, PET Bottles, Aluminium Cans, Aerosol Cans
Weima A. Series Label Press
Our hydraulic drainage presses dispose of old labels in bottling facilities efficiently and economically. The WEIMA A.200 produces pressed labels with an output diameter of 200 mm. Discharged labels are first picked up by the label press, then pressed and finally transported drip-free into a container.
Robust technology through simple hydraulic compaction
Machines of the WEIMA A series have a particularly robust design. The design is comparatively simple and gets by with few electronics. In contrast to screw presses, only a few moving parts are installed. Thus, even with many years of use, wear is minimal.
Dimensionally stable discs due to angled discharge tube
The discs are formed by the press cylinder, which presses the material against the previously produced discs, which are still in the discharge pipe. The angled bend of the discharge pipe generates enough counterpressure to strongly compact and drain the material. In addition, the wedge position of the discharge pipe can be used to set subsequent recompaction.
Resistant to foreign materials without clogging
Due to the robust machine design, WEIMA label presses are particularly resistant to contaminants. In contrast to screw presses, presses of the A series cannot block mechanically and simply press dangerous foreign materials such as bails of swing-bottle glass bottles into the pressed product. This way, clogging or jamming of the machine can be avoided.
Simple program adjustments through PLC control
The built-in PLC control is optimally adapted to the drainage process. Many settings, such as the press force and cycle time, are preset but can be easily adapted to the desired application. If required, the machine can be used in manual or automatic mode. We use only high-quality brand components – for example from Siemens, Allen Bradley or Rittal.
Targeted collection and discharge of lye with lye collection tray
The caustic pressed out during the pressing process is collected in the lye collection tray. From there, the liquid can be discharged in a targeted manner – into the drain or to the caustic recirculation system. The connection option can be defined individually according to customer requirements.

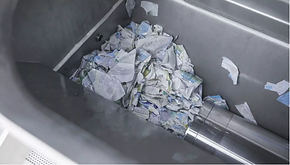

Example of WEIMA Drainage Press and WEIMA Shredder process line

WEIMA - G.300 Duo Series
WL Shredder
Hygienic design separated material for rework
Control Unit