WESTERIA – leading the world in Windsifter technologies


Westeria Airstar dual installation

Finished compost with high degree of purity after being treated by the AirLift at Lübeck municipal waste department’s biomass plant.
WESTERIA is a German company with over 60 years of experience producing innovative machinery. Manufacturing conveying and windsifting technology designed for Waste to Energy and Recycling industries, WESTERIA are leading the way towards making circular economies valuable around the world.
The patented windsifting solution from Westeria – the technological leader – allows the separation of the heavy fraction (contaminates) from the light fraction in one easy step.
These machines are integrated into recycling systems post shredding and screening to separate high value material from contaminates such as rock, gravel, nonferrous material etc.
WESTERIA offers a wide range of designs that can separate materials into 2, 3 or even 4 different fractions. Machines are compact with low energy consumption and can be delivered as stationary, semi-mobile or mobile solutions.
WESTERIA Windsifters can be found in over 500 installations worldwide with varying applications including;
-
MSW
-
C&D
-
Post-Industrial waste
-
Composting sites
-
RDF production
-
MRF and PRF
-
PET bottle Recycling
Key advantages of WESTERIA machines are;
-
Higher efficiency than normal over belt suction systems
-
Precise adjustment of ballistic flight curve, air velocity and viewing gap
-
Higher purity levels of more than 99 %. Maximal throughput 320 m3/h
WESTERIA delivers what it promises: best separation results, low and easy maintenance, reliability, and durability.

Airstar®
The original Cross-Flow Wind Sifter for all heavy-light separation applications.
Including:
1. Alternative Combustibles Processing
-
Efficient separation of all impurities for the secondary shredding
-
Reduction of wear costs for secondary shredders
-
Damages at the secondary shredder are avoided
-
Increase of calorific value of alternative combustibles
2. Mixed Construction Waste Processing
-
Production of a recyclable stone fraction
-
Extreme cost reduction for waste / landfill
-
Reduced effort for processing of residuals
3. Slag Processing
-
Production of a valuable heavy fraction
-
Reduced effort for processing recyclable material
-
Relief of NIR- and FE-separators
-
Reduction of landfill costs
With a working width up to 3m, the AIRSTAR™ can process up to 400m3/hr of material, while the addition of a DISC SPREADER ensures the full working width of the acceleration belt is utilized.
The acceleration belt runs at 3m/s and comes standard with a heavy-duty built-in impact zone, which prevents damage to the load bearing rollers. The automatic belt tracking system keeps the maintenance and belt wear to a minimum. Further, the clever suspension design, allows adjustment of the belt horizontally and vertically from one point, with an optional automatic adjustment system to simply change process settings through an integrated touch screen control.
The acceleration conveyor operating at 3m/s delivers the 1st part of the separation through singulation of the material. Next the adjustable airflow carries material towards and over the heavy duty separation drum. Heavy material and if desired, hard objects that bounce of the drum, are therefore effectively separated from the lights.
The nozzle design is designed to deliver even airflow and speeds across the width of the machine, therefore achieving 60% higher core jet speed then comparable Windsifter whilst using less energy.
The rotating drum features an axle-less internal drive system which prevents the possibility of material jamming or wrapping in-between the drum and the frame. Multiple access points via gas-struts supported doors, fitted with safety switches, ensure ease of maintenance and cleaning.
The drum also comes standard with a spring-loaded scraper to stop wet material building up on the surface.
The modular design and flexibility of the system allows for either 2 or 3 way material splits. (Heavy, Light, extra light), through the use of an adjustable shuttle conveyor after the drum, collecting the different materials following their density.
Operation is easily and safely observed via the large glass doors and windows located along the full length of the machine. Designed with transport in mind the complete system is modular and can be packed into standard shipping containers. Simple and clear assembly instructions allow for on site assembly in a matter of days.

AirBasic®
The AirBasic brings the advantages of our proven windsifting technology to a small, mobile machine.
It is available in various options to ensure optimum separation results at any site. The material can be fed from any direction (180°). The AirBasic features a patented adjustable and precise nozzle system that works much more efficiently than comparable products on the market.
The main part of this machine consists of a two-way separation system, where conveyors or other modules like the AirLift or DiscSpreader can be easily integrated to adapt it to your needs.

Airlift®
AirLift uses the diametric downflow principle in the settling chamber to ensure still more precise separation of the various fractions in a second stage.
The SPEEDCON high-speed conveyor belt, which has a particularly long design service life, feeds the material at up to 4 ms-1 to the central element, the AirLift. The AIRWHEEL™ is arranged downstream of the AirLift.
Depending on model, possible working widths of the AirLift range between 1,000 mm and 3,500 mm, the widest being capable of handling throughputs of up to 320 m³/h with a grain size of 60 mm to 250 mm. Maximum outlet capacity is 5.6 t/h. Automatic gate controllers prevent material blockages on the input and the output sides and so ensure high operational reliability. Being continuously adjustable, such automatic gate control also ensures that the passage height can be exactly adjusted to the specific separation goal.


Airlift® move
The AirLift move brings effective separation to any location. The mobile version of our widespread over belt windsifter frees your material from impurities as uncomplicated as never before.
The ultra-light separator is already widely used as a stand-alone version for the removal of impurities. Materials with similar specific densities are easily separated by the unit. For compost processors, the AirLift move therefore enables the effective and efficient removal of films from the valuable organic material.
Airwheel®
AIRWHEEL™ rotary screening drum separates the ultra-lights from the air stream.
The AIRWHEEL™, allows for exhaust air to be separated from the extra light material without sending all the extra lights to a bag house therefore reducing blockages. The AIRWHEEL™, is self-cleaning via an internal scraper and cleaning bar.
The fan is enclosed inside the machine to reduce noise and installation time. Intake air can be drawn directly from around the unit or ducted from an external location. The residual dust-air mixture is fed into a dust filter.
Case Study – AIRSTAR™ plus AIRWHEEL™ - Doyle Bros, NSW, Australia
With limited space in their existing building, Doyle Bros turned to Westeria to meet their separation requirements. An AIRSTAR 1500 – L1 , short chamber with 20° inclination, was installed to sort heavy material (metals, glass, stones, etc.) before the material goes forward an to NIR machine. A high speed secondary shredder that follows needs to be protected against these heavy materials.
The addition of the AIRWHEEL 15, an air filter for trapping and separating light material such as film plastics, makes the extreme short design possible by guaranteeing that light material is separated out and only fine (4mm minus) particles reach the baghouse, serving as a protection device for the baghouse.
After a pre screening step through SPALECK screen, which removes 0-30mm material, the Doyle Bros machine can handle up to 150m³ of material per hour.
The material separation after the AIRSTAR™ and AIRWHEEL™ combination is near perfect, allowing the light fraction conveyor to directly feed the acceleration conveyor into the NIR.
Doyle Bros is among hundreds of customers from around the world can confirm that the AIRSTAR™ from WESTERIA delivers what it promises: best separation results, low and easy maintenance, reliability, and durability.
In Australia the WESTERIA machines are supplied, supported, and serviced through CEMAC technologies
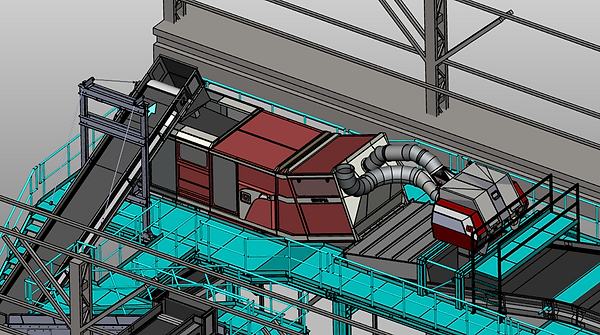
Illustration of Doyle Bros AIRSTAR and AIRWHEEL installation

Conveyor for pre screened material feeding the AIRSTAR

AIRWHEEL light fractions being fed directly onto NIR conveyor